87xjco
NAXJA Forum User
- Location
- Denver, CO
Daniel's (xjeepers2) XJ
is getting this full width HP44 and a Ford 9"
He has a Full Traction 6" lift kit and 33" tires and he plans to go to 37"
He brought me the axles for the gear install and the rest of the build.
The build will get
5.13 PORC gears
Lockrite locker
Parts Mike 1 ton TRE's and 1/4" wall dom tie rod and drag link , mounted over the knuckle
TnT truss, spring perches, control arm brackets, and over the knuckle track bar bracket
New Ball joints
New spicer u-joints
Knuckle rotation
New rotors pressed on the existing hubs
First I did some teardown so I can start determining how far to rotate the knuckles
Daniel found a leaf sprung HP44 from probably a 78 or so F150 Ford truck
TnT now makes the truss that works with this center section that has the cast leaf spring mount integrated into it
I pulled the caliper and rotor off, the Ford spindle is a 5 bolt spindle unlike Chevy and Waggys that have 6 bolt spindles
Knocked the spindle off and now the axle can slide out
Then the ball joint nuts were removed and a few whacks with a big hammer and the knuckle is off
So I'll start checking some angles. First I made sure the housing was level on my cart
And at the same time I set the pinion angle to 7 degrees (o/k 7.1 degrees, 90 degrees vertical minus 82.9 degrees equals 7.1 degrees) This will be close for now until I figure out exactly what pinion angle is needed.
Edit - it ended up being 7.2 degrees
Then I measured at the flat surface of the inner C on both the upper and lower ball joint areas
Probably the lower is the most accurate, + 1.9 degrees caster
Then I made an index mark on the tube and the knuckle
I'm going to use that index mark as a crude measurement to help me position that inner C, and I'll confirm it with the digital level
I've done the math (probably wrong though:scared: ) and one degree of rotation equals .0026175"
So 4 degrees rotation will equal .0104" or just over 1/10"
I guess that shows why it's so easy to be off a degree or so when doing a knuckle rotation, when 26 thousandths equals 1 degree
I always like to refresh my memory and make sure I have positive and negative caster right in my head
I'll talk more later about how I figured out that I need 7.2 degrees pinion angle
With the pinion at 7.2 degrees, I know the inner C's need to be rotated about + 4.0 degrees, I want them to end up at somewhere around + 6 degrees +/- 1 degree.

is getting this full width HP44 and a Ford 9"
He has a Full Traction 6" lift kit and 33" tires and he plans to go to 37"
He brought me the axles for the gear install and the rest of the build.
The build will get
5.13 PORC gears
Lockrite locker
Parts Mike 1 ton TRE's and 1/4" wall dom tie rod and drag link , mounted over the knuckle
TnT truss, spring perches, control arm brackets, and over the knuckle track bar bracket
New Ball joints
New spicer u-joints
Knuckle rotation
New rotors pressed on the existing hubs
First I did some teardown so I can start determining how far to rotate the knuckles
Daniel found a leaf sprung HP44 from probably a 78 or so F150 Ford truck

TnT now makes the truss that works with this center section that has the cast leaf spring mount integrated into it

I pulled the caliper and rotor off, the Ford spindle is a 5 bolt spindle unlike Chevy and Waggys that have 6 bolt spindles

Knocked the spindle off and now the axle can slide out

Then the ball joint nuts were removed and a few whacks with a big hammer and the knuckle is off

So I'll start checking some angles. First I made sure the housing was level on my cart

And at the same time I set the pinion angle to 7 degrees (o/k 7.1 degrees, 90 degrees vertical minus 82.9 degrees equals 7.1 degrees) This will be close for now until I figure out exactly what pinion angle is needed.
Edit - it ended up being 7.2 degrees

Then I measured at the flat surface of the inner C on both the upper and lower ball joint areas

Probably the lower is the most accurate, + 1.9 degrees caster

Then I made an index mark on the tube and the knuckle

I'm going to use that index mark as a crude measurement to help me position that inner C, and I'll confirm it with the digital level
I've done the math (probably wrong though:scared: ) and one degree of rotation equals .0026175"
So 4 degrees rotation will equal .0104" or just over 1/10"
I guess that shows why it's so easy to be off a degree or so when doing a knuckle rotation, when 26 thousandths equals 1 degree
I always like to refresh my memory and make sure I have positive and negative caster right in my head
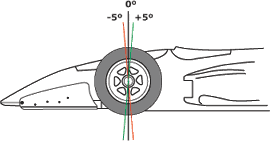
I'll talk more later about how I figured out that I need 7.2 degrees pinion angle
With the pinion at 7.2 degrees, I know the inner C's need to be rotated about + 4.0 degrees, I want them to end up at somewhere around + 6 degrees +/- 1 degree.