anthrax323
NAXJA Forum User
- Location
- San Antonio, TX
Not sure this is the right place for it, but being a non-red member I can't toss it up in Advanced Fabrication & Engineering (not that this would even qualify).
In any case, I recently joined TechShop here in Raleigh and got my MIG and general metal shop SBU (safety and basic usage) classes out of the way and went to work...
You can probably make out a few of the more awful welds in the first and last pictures... I attempted to miter joint 1.25" x 0.125" angle steel after cutting it using a large horizontal bandsaw (which had no built-in protractor, nor any good planes against which to really set the angle correctly with a handheld one).
In any case, the middle two pictures are taken of the same union... One front, one back. I'd consider those to be the welds I'm laying down consistently after figuring out the ideal voltage and wirefeed speed settings for this particular material (had to go cooler, as the line between good penetration and burning through was far too fine). The last picture is the first weld I did on this piece (and first weld I ever did alone), which also shows my horrible, horrible gap filling attempt...
So, if you've got any welding experience... How does this look for a first time 'round the block? I think that even with this project included, I haven't laid more than 24" of weld to date (but will be doing more once I can chop up some angle steel on a proper miter saw) so I'm very, very much in the learning process. Any and all tips/criticisms are greatly appreciated!
In any case, I recently joined TechShop here in Raleigh and got my MIG and general metal shop SBU (safety and basic usage) classes out of the way and went to work...
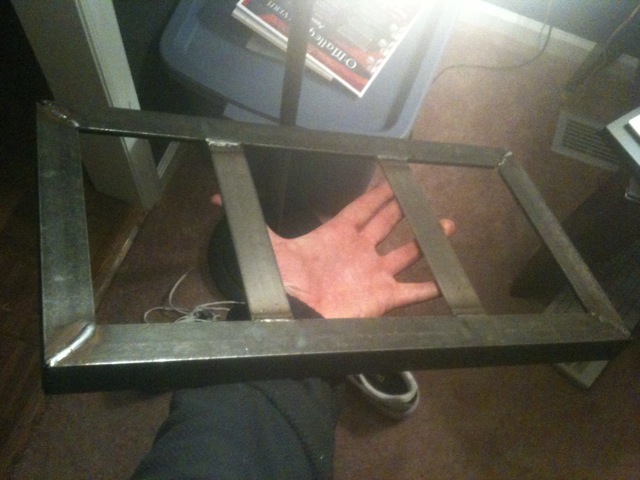
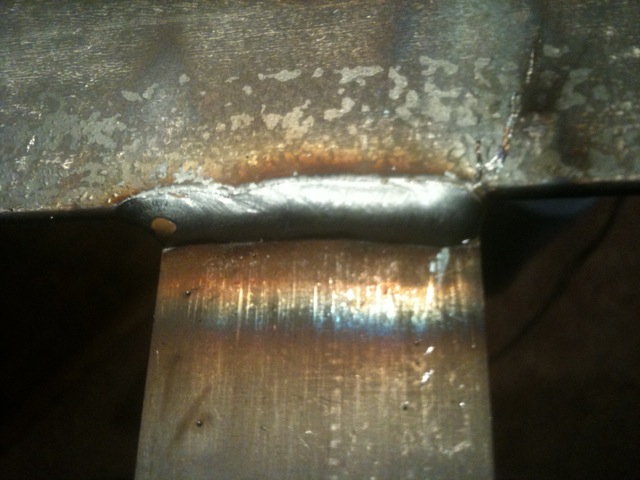
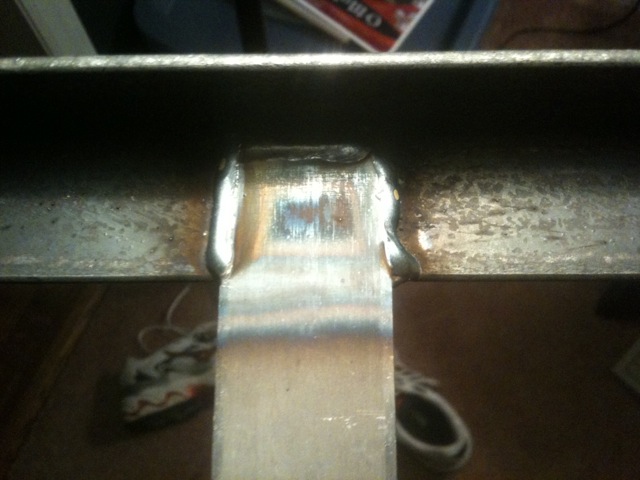
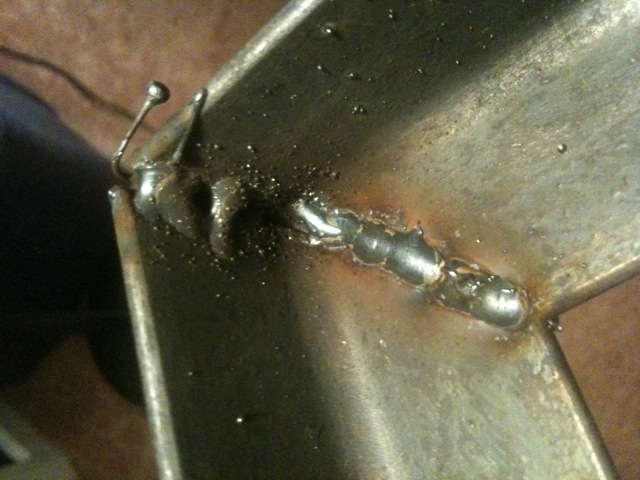
You can probably make out a few of the more awful welds in the first and last pictures... I attempted to miter joint 1.25" x 0.125" angle steel after cutting it using a large horizontal bandsaw (which had no built-in protractor, nor any good planes against which to really set the angle correctly with a handheld one).
In any case, the middle two pictures are taken of the same union... One front, one back. I'd consider those to be the welds I'm laying down consistently after figuring out the ideal voltage and wirefeed speed settings for this particular material (had to go cooler, as the line between good penetration and burning through was far too fine). The last picture is the first weld I did on this piece (and first weld I ever did alone), which also shows my horrible, horrible gap filling attempt...
So, if you've got any welding experience... How does this look for a first time 'round the block? I think that even with this project included, I haven't laid more than 24" of weld to date (but will be doing more once I can chop up some angle steel on a proper miter saw) so I'm very, very much in the learning process. Any and all tips/criticisms are greatly appreciated!
Last edited: