SC Rednek
NAXJA Forum User
- Location
- Winchester TN
I'm not quite done yet, figured I'd post up some pictures and get any opinions before I finish in the next few days. I've got a '99 with an AX15, just finished welding on frame stiffeners from Brian (HD Offroad Engineering).
I bought a new poly trans mount since mine had 200k miles on it, if you want to replace your stock mount on an AX15 '98-'01 don't order from rusty's! It won't fit! But I planned on building a new crossmember anyway since my old one was was rather bent from bashing it on rocks, so I don't care, it actully worked to my advantage. I've always had good experiences and customer service with rusty's before, and if I'd complained about this I'm sure I could have gotten full customer satisfaction from them, this is not the point of the thread so please don't get side tracked, I know some of you don't like rusty's but I do I've ordered from them plenty of times and think they're just fine.
I got a 4' x 2" x 4" box tube and a 4' x 1/4" x 3 1/2" strap, I was only able to get 14 gauge tube, if anyone knows any good scrap steel yards here in Vegas it would be appreciated, I can't find any (I just moved here though). The new trans mount had upper bolt holes to work either on the transmission directly, or on the factory relocation bracket to make it work (I'm assuming, I don't own one) on the same crossmember as the longer AW4, but the new mount is too short and a different lower bolt pattern to work with the stock crossmember. I decided to mount it on the trans directly, since this would make the bottom exactly level with the frame rail, giving me more clearance. Like this
This is the start of my crossmember. I plan on welding nuts to a plate attached to the exposed end of the 2x4 tube on the inside of the frame rail, with some small round tube cut down as spacers between the inner side of the rail and the plate, so the crossmember is bolted through the rail, not to the bottom of it like from the factory, so more strength bolted through 3 layers of frame(frame stiffy and rail) and 2 layers of crossmember, instead of 1 each, and no risk of bashing the bolt heads on rocks.
I welded the 1/4" strap to the bottom to reinforce and protect it, the section under the frame rail and the mount itself are particularly weak otherwise and I was worried about twisting. I plan on welding another 1/4" plate under the mount itself, and using a 1" hole saw around the mount bolt holes, that 1/2" of depth should protect the nuts on the bottom of the trans mount. Here's a picture of my current progress, I've got the 1/4" strap welded on the bottom.
Any suggetions before I finish it up? Think it'll be strong enough? Or should I modify anything before I finish up?
I bought a new poly trans mount since mine had 200k miles on it, if you want to replace your stock mount on an AX15 '98-'01 don't order from rusty's! It won't fit! But I planned on building a new crossmember anyway since my old one was was rather bent from bashing it on rocks, so I don't care, it actully worked to my advantage. I've always had good experiences and customer service with rusty's before, and if I'd complained about this I'm sure I could have gotten full customer satisfaction from them, this is not the point of the thread so please don't get side tracked, I know some of you don't like rusty's but I do I've ordered from them plenty of times and think they're just fine.
I got a 4' x 2" x 4" box tube and a 4' x 1/4" x 3 1/2" strap, I was only able to get 14 gauge tube, if anyone knows any good scrap steel yards here in Vegas it would be appreciated, I can't find any (I just moved here though). The new trans mount had upper bolt holes to work either on the transmission directly, or on the factory relocation bracket to make it work (I'm assuming, I don't own one) on the same crossmember as the longer AW4, but the new mount is too short and a different lower bolt pattern to work with the stock crossmember. I decided to mount it on the trans directly, since this would make the bottom exactly level with the frame rail, giving me more clearance. Like this

This is the start of my crossmember. I plan on welding nuts to a plate attached to the exposed end of the 2x4 tube on the inside of the frame rail, with some small round tube cut down as spacers between the inner side of the rail and the plate, so the crossmember is bolted through the rail, not to the bottom of it like from the factory, so more strength bolted through 3 layers of frame(frame stiffy and rail) and 2 layers of crossmember, instead of 1 each, and no risk of bashing the bolt heads on rocks.
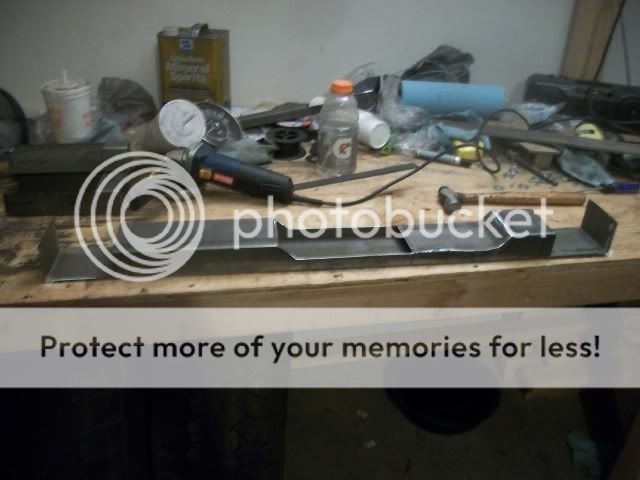
I welded the 1/4" strap to the bottom to reinforce and protect it, the section under the frame rail and the mount itself are particularly weak otherwise and I was worried about twisting. I plan on welding another 1/4" plate under the mount itself, and using a 1" hole saw around the mount bolt holes, that 1/2" of depth should protect the nuts on the bottom of the trans mount. Here's a picture of my current progress, I've got the 1/4" strap welded on the bottom.
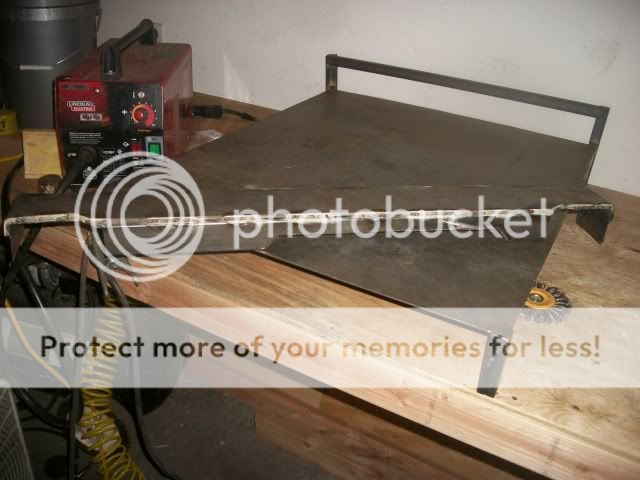
Any suggetions before I finish it up? Think it'll be strong enough? Or should I modify anything before I finish up?
Last edited: