Some updates:
Some steel arrived this past week (no... the pipe isn't mine :laugh2: )
I made some templates and then cut up some 1/8" steel plate to make some really long fish plates to enforce the replacement rail joint. Two of the plates are also to go down the side to the location of where the front of the leaf spring used to mount. I've still got to make some for the inner side of the rail to enforce where the links will mount.
After numerous calculations I couldn't get the supplied brackets that came with the BTF D60 rear truss system for the upper link mounts on the axle side to work. They really needed to be 1.5" taller.
So I made some of my own (no way in hell I'm gonna pay $5+ for a simple bracket). Everything below is 1/4".
I've probably got way to much time into these, but I'm sure they'll hold up! I made some braces for between them, they will also probably get gussets on the outside. Not welded yet, just sitting together with magnets.
I also measured and made up some frame side brackets for the rear links. Who says the average DIY'er can't have fancy slotted brackets? Just gotta make them. :thumbup:
Lowers (upside down):
Uppers, two holes in these as it leaves room for one of two different 4 link setups to figure out what works best.
That's it for now. I've still got to make the 1/8" plates that will brace the inner side of the unibody rail so the link brackets don't tear off. I'm thinking that plating the unibody with 1/8" and welding the brackets to that should be fine. Right? :dunno:
As for links, the plan is as follows:
2-5/8", 1.25" shank Currie Johnny Joint on one end of the link, and a welded greaseable bushing on the other for all links.
Lowers: 2"x.500" wall or 2"x.250" wall
Uppers: 1.75"x.375wall
Some steel arrived this past week (no... the pipe isn't mine :laugh2: )
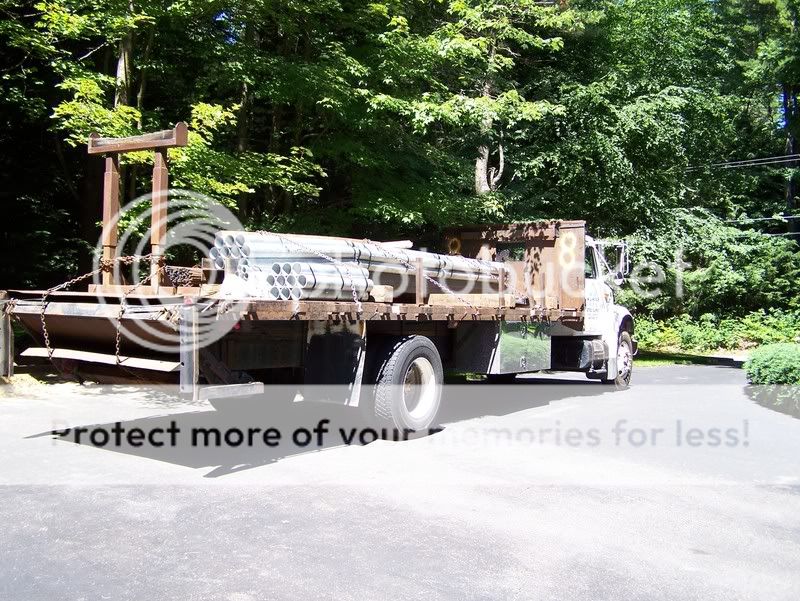
I made some templates and then cut up some 1/8" steel plate to make some really long fish plates to enforce the replacement rail joint. Two of the plates are also to go down the side to the location of where the front of the leaf spring used to mount. I've still got to make some for the inner side of the rail to enforce where the links will mount.
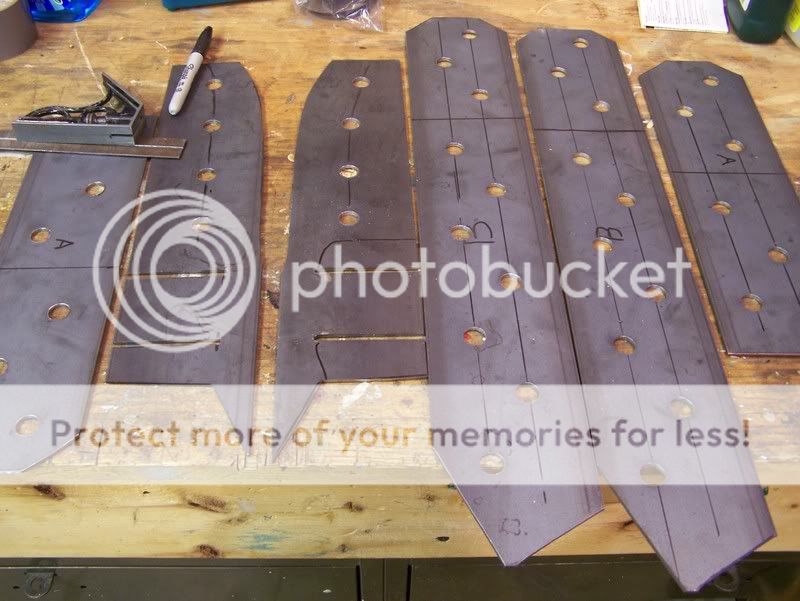
After numerous calculations I couldn't get the supplied brackets that came with the BTF D60 rear truss system for the upper link mounts on the axle side to work. They really needed to be 1.5" taller.
So I made some of my own (no way in hell I'm gonna pay $5+ for a simple bracket). Everything below is 1/4".
I've probably got way to much time into these, but I'm sure they'll hold up! I made some braces for between them, they will also probably get gussets on the outside. Not welded yet, just sitting together with magnets.
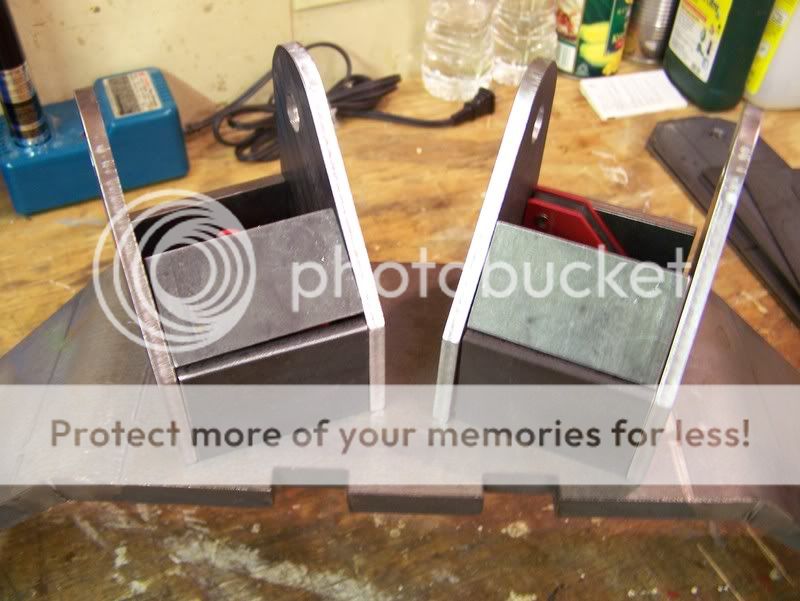
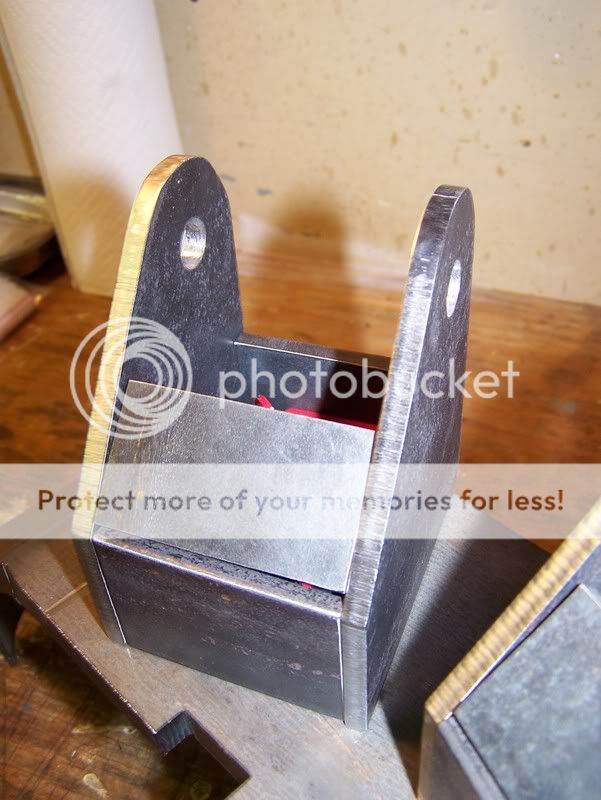
I also measured and made up some frame side brackets for the rear links. Who says the average DIY'er can't have fancy slotted brackets? Just gotta make them. :thumbup:
Lowers (upside down):
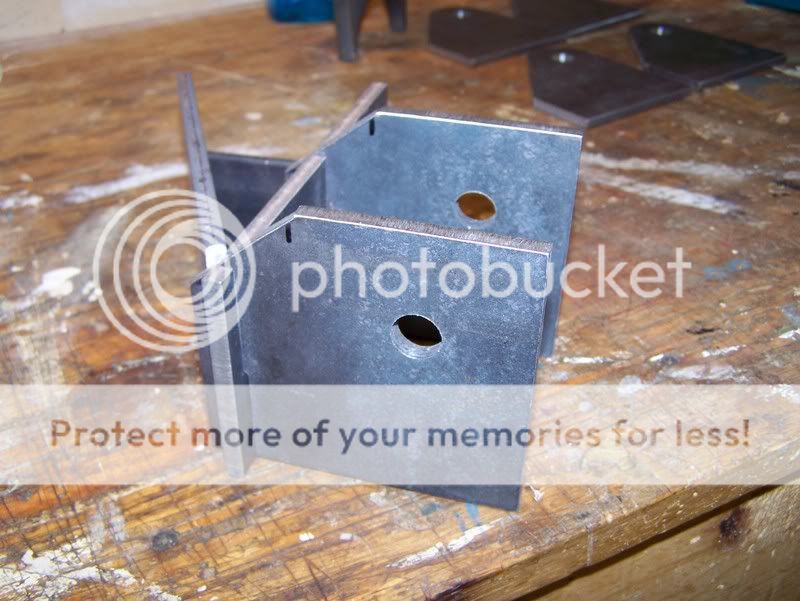
Uppers, two holes in these as it leaves room for one of two different 4 link setups to figure out what works best.
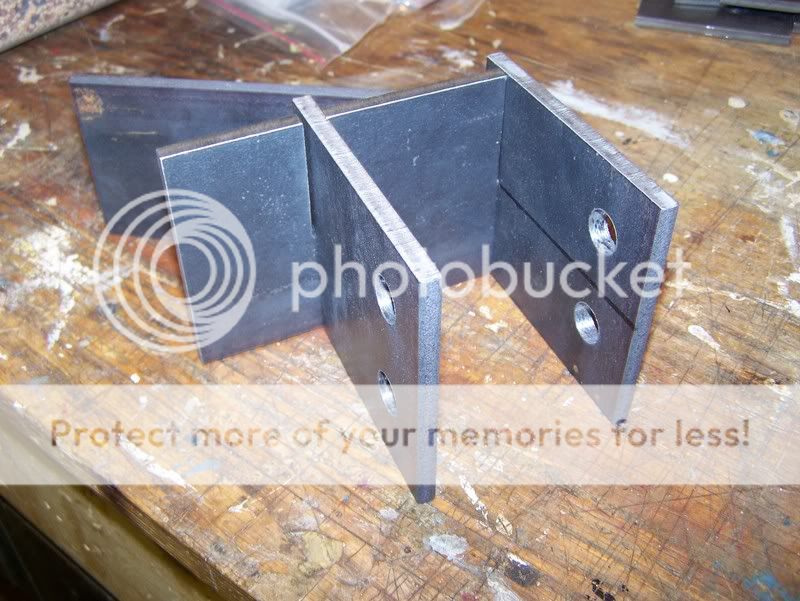
That's it for now. I've still got to make the 1/8" plates that will brace the inner side of the unibody rail so the link brackets don't tear off. I'm thinking that plating the unibody with 1/8" and welding the brackets to that should be fine. Right? :dunno:
As for links, the plan is as follows:
2-5/8", 1.25" shank Currie Johnny Joint on one end of the link, and a welded greaseable bushing on the other for all links.
Lowers: 2"x.500" wall or 2"x.250" wall
Uppers: 1.75"x.375wall
Last edited: