XJfire75
NAXJA Forum User
- Location
- Toonnerville, GA
Hey guys I made a hitch for my XJ. I only spent $31 and used scrap steel other than the reciever tube I bought.
Made the mounting plates from 2"x3"x1/4" angle and main tube is 2"x2"x1/4" tubing with the 2 1/2" square reciever. Along with some 3/16" gussets and 1/4" gussets.
4- 1/2"-13x 1 1/2" bolts and 3- 12mm on the stock nut strip.
Heres the pics.
Think it'll hold up?
The hitch's main tube will only stick below the bumper 1" and the reciever tube sits flush against the taper of the bumper for a good tight fit.
Welded everything...twice LOL
welding the stock mounts to the angle for a stronger bumper as well.
Recessed the reciever into the 2"2"x1/4" main tube 1" and welded and gusseted all around. The weakest link will be the bolts...All 6 of them 1/2" ha
3/16" gussets 5"x5" welded inside and out. Slotted mounting holes for fine tuning the mounting. Worked out good.
Safety chain holes and 1/4" gussets. Welded once again front anc back and to the reciever tube up and down LOL
End result.
Made the mounting plates from 2"x3"x1/4" angle and main tube is 2"x2"x1/4" tubing with the 2 1/2" square reciever. Along with some 3/16" gussets and 1/4" gussets.
4- 1/2"-13x 1 1/2" bolts and 3- 12mm on the stock nut strip.
Heres the pics.
Think it'll hold up?
The hitch's main tube will only stick below the bumper 1" and the reciever tube sits flush against the taper of the bumper for a good tight fit.
Welded everything...twice LOL

welding the stock mounts to the angle for a stronger bumper as well.

Recessed the reciever into the 2"2"x1/4" main tube 1" and welded and gusseted all around. The weakest link will be the bolts...All 6 of them 1/2" ha
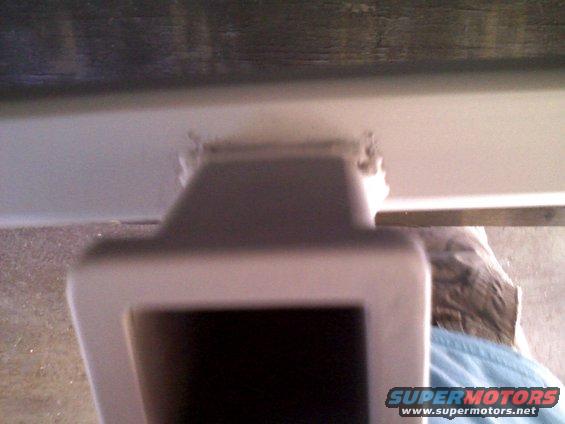
3/16" gussets 5"x5" welded inside and out. Slotted mounting holes for fine tuning the mounting. Worked out good.
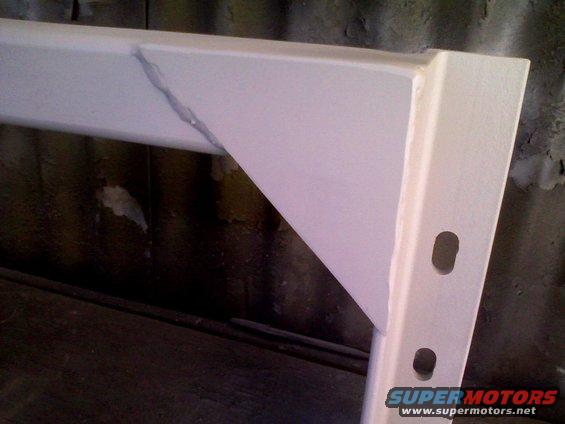
Safety chain holes and 1/4" gussets. Welded once again front anc back and to the reciever tube up and down LOL
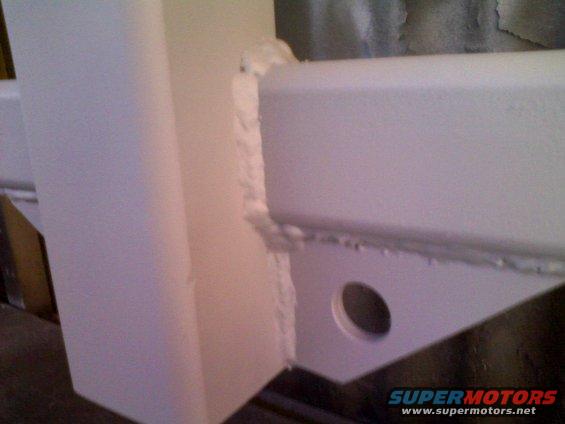
End result.
