I had some free time in my auto class, so I fooled around with their mig. Its nice using gas. Here are some pics of my welds.
Welder was a Lincoln 110v 140 amp mig with argon/co2 mix
Please critique my welds. In the pics, I was welding .120 wall tube to 1/4" flat plate.
Any input will be greatly appreciated!

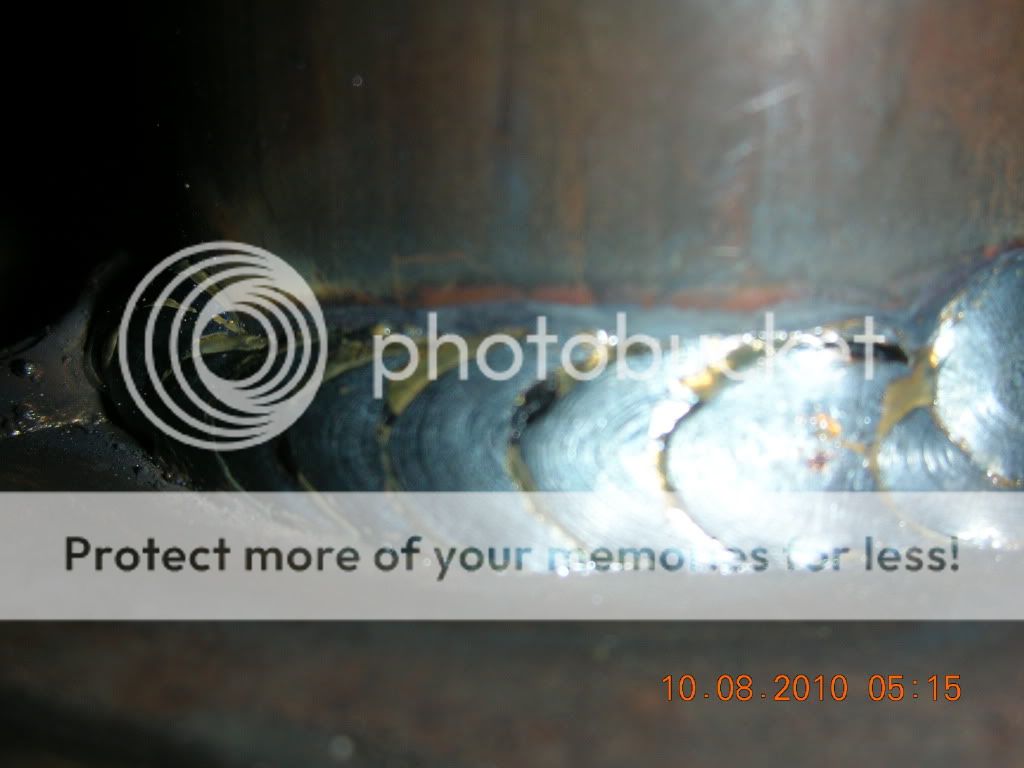

Welder was a Lincoln 110v 140 amp mig with argon/co2 mix
Please critique my welds. In the pics, I was welding .120 wall tube to 1/4" flat plate.
Any input will be greatly appreciated!